
RICO Manufacturing Inc.
691 West Liberty St.
Medina, Ohio 44256
ricoequipment.com
A lift truck is a piece of equipment that allows an individual person to move heavy objects. Lift trucks reduce the number of people needed to move materials, is a safe way to handle large loads, and increase efficiency as loads are moved more quickly. But there is a big difference if you need to move a jet engine after it has been completed or you need to move large coils of steel and can’t make a dent in the metal. RICO Manufacturing employs a team of engineers who design each lift truck to the needs of the customer and makes sure it is exactly what is needed. For example, lift trucks used in areas with flammable materials have to be specially made so they don’t cause sparks. And if there is something that happens, RICO lift trucks are explosion-proof!
View RICO Manufacturing’s Timeline Here
How did the business start?
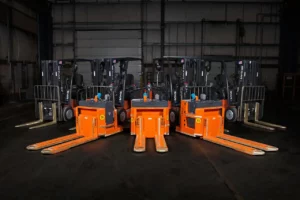
Boyd Ross was working for a large lift truck manufacturer when he decided to go out on his own. At the company where Ross worked, everyone used the exact same lift trucks and he knew it would be even better if the truck was customized to the job. In 1984 he launched RICO Manufacturing to do just that. His first product was a die handler. A die is similar to a mold and in this case was used to make metal into shapes. When it was time to change the die, workers had to shut down the press, manually remove the die, manually put in the new die, and start the press back up. It was often dangerous work and required a number of people to perform the operation. With the customized lift truck, the job could be done by one or two people and the danger was reduced siginificantly.
What challenges are you facing?
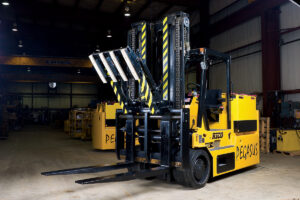
We need people with special training – typically engineers to design the lift trucks, mechanics to fix them, etc. and it is tough to find those people. They typically have a job already. We also are seeing a big increase in costs in both raw materials and finished goods. That means things we get in that we have to make into something, like steel, is more expensive, and parts we get from other companies are more expensive. We have to determine how much of that increase in cost we can pass on to our customers.
Where are your customers and suppliers located?
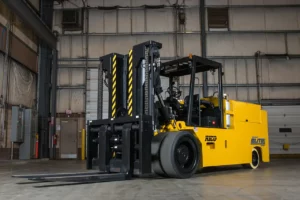
100% of the steel we use is made in the United States. We get parts from all over the world because there are a lot of specialized parts in our lift trucks so we need the best there is. We also sell all over the world and our customers come to us for all kinds of solutions.
Does your company focus on any sustainability efforts?
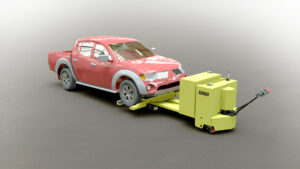
We practice Lean Manufacturing which is the idea that you maximize efficiency while minimizing waste. Waste is considered anything the customer isn’t paying for and / or that doesn’t add value to the product. So for example, if you got paid to write a paper, you would charge your customer for the time it took you to do any research needed and to write the paper, whatever you used to write the paper (actual pen and paper or a computer, etc.), and some portion of what it costs you to pay for electricity, etc. But you couldn’t charge the customer for paper you used that was then recycled because you made a mistake. That is the kind of waste we work hard to reduce. So we are always looking for ways to minimize what we have to recycle or throw away.
How does your business interact with government?
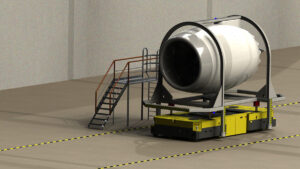
We work closely with the military and provide lift trucks to all branches of the armed forces. Contracts with the military are more complicated, typically, than with companies because everything is reviewed by a number of people. We also have to be able to explain anything we charge, etc. We are also very aware that all the money used to pay for our equipment is tax money and we want to be responsible with that as well.
How does someone get a job
with you?
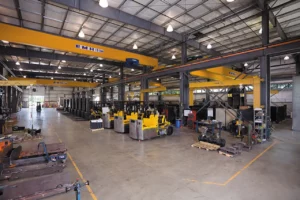
All of our positions are posted on our website and through other job boards. In our business we have positions that require college degrees in engineering, for example, or certifications if you are a welder, and we have office positions in marketing, human resources, finance, and others. So we have a wide range of positions that might be available at any given time.
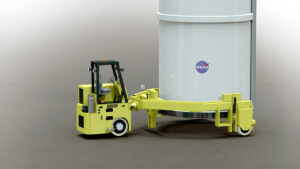
Wondering what that picture is? It is designed to handle sections of solid rocket boosters. They are 12 feet in diameter, 20 feet tall, and weigh more than 12,000 lbs! What could those be used for? Originally, this was designed to help with space shuttle launches!
Why do employees like to work here?
We never have the same day twice. Each project is unique in some way and we work as a team to build each one. We aren’t constantly focused on the number of parts we’re trying to get out the door because when we are done, we have a customized lift truck that is complete going out the door. It gives our employees a feeling of pride in their work and they can easily see how what they do fits into the final product. We also reward hard work in a variety of ways because we value our team.